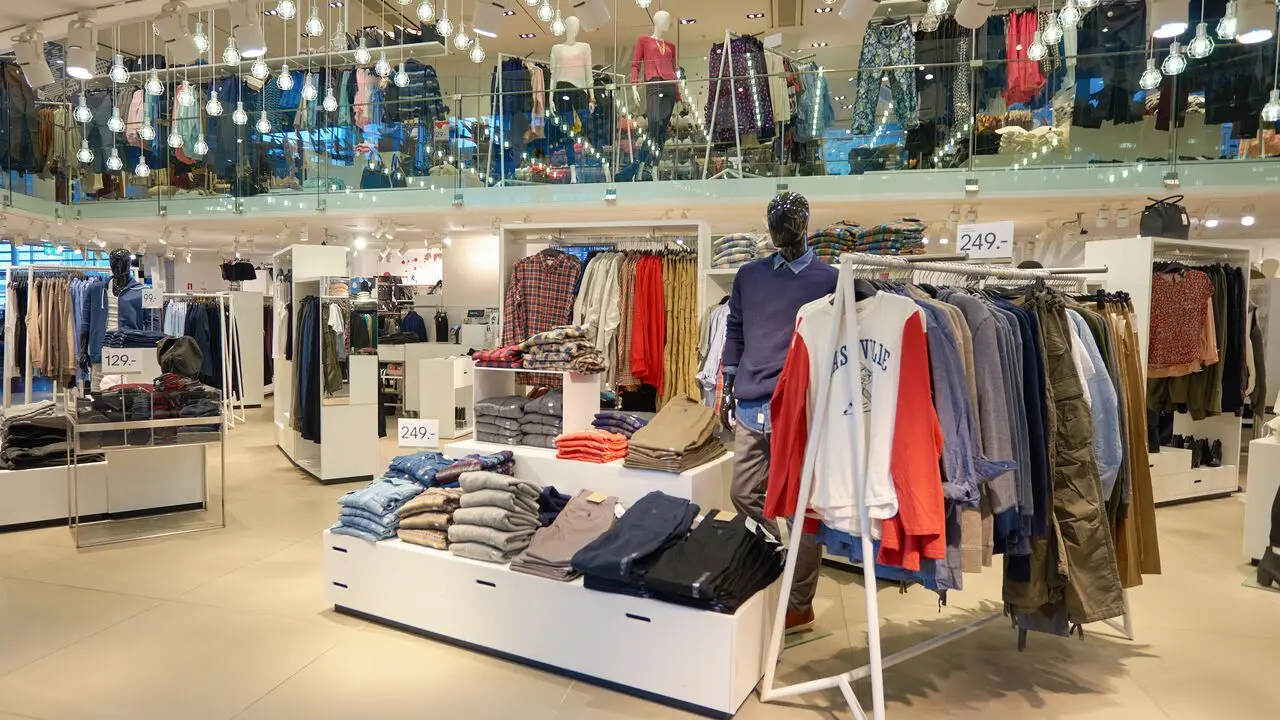
As illustrated earlier, textile production is a complex process, and recycling involves retracing several steps in the production chain and, to some extent, repeating them. Consequently, there isn’t a single recycling strategy; end-of-use textiles can re-enter the process chain at various points (i.e., as fibers, polymers, or monomers), requiring at least part of the process chain to be traversed again (compare Figure 2). Therefore, the recycling route should aim to go back as little as possible to minimize the repetition of process steps. Brief explanations of potential cycles are outlined below.
1. Production of Cleaning and Wiping Rags (CWR):
This process involves minimal alterations (e.g., cutting into approximately 20 x 20 cm pieces) to the physical and chemical properties of textiles. The manufacture of CWR requires low energy as no additional processing than cutting is needed. However, these CWR are disposable products that undergo thermal recovery after use. Thus, this route does not align with the circular economy concept.
2. Recycling while Maintaining Fiber Structure:
This involves disassembling the textile structure while retaining the integrity of fibers. Tearing machines can be employed to generate fibers suitable for yarn or non-woven fabric manufacturing. A consequential reduction in fiber length, and consequently a potential decrease in quality, is frequently unavoidable. As an alternative, textiles can be transformed into flock, consisting of short (non-spinnable) fibers suitable for incorporation as additives in construction materials. In both scenarios, the necessity for initiating new fiber production is obviated, leading to significant energy savings.
3. Recycling Maintaining the Underlying Polymer:
Physical properties are altered (e.g., melting or dissolving), while maintaining the chemical structure. The melted or dissolved polymer is introduced into a fiber spinning process. For instance, cotton textiles can serve as raw material for producing lyocell fibers, substituting native wood, resulting in recycled fibers equivalent to those from new raw materials. Secondary thermoplastic polymers, such as PET, can also be fed into a melt spinning process.
The main challenge for this process is the need for high-purity input streams, contrasting with textiles containing multiple polymers. High-quality sorting and/or additional separation steps (mechanical, chemical, biochemical) are essential but not yet industrially implemented. Compared to the previous routes, the energy-saving potential is lower as a significant portion of the processing chain has to be redone.
4. Recycling at the Level of the Underlying Monomer(s):
This involves physically and chemically altering the fiber. For example, fibers from PA6 can be converted to polycaprolactam, which is then used for a new polymerization to PA6. While suitable for a wide range of input materials, this route requires almost the entire process chain to be revisited.