Optimize 2024, presented by Aspen Technology, Inc. (AspenTech; Bedford, Mass.) on April 29 -May 3 in Houston, featured a keynote panel on May 1 entitled Navigating Net Zero: Unleashing Advanced Technology and Collaborative Partnerships. This event brought together sustainability leaders from across the process and power industries to discuss their organizations’ strategies and progress. Rasha Hasaneen, chief product & sustainability officer at AspenTech moderated the panel (photo), which included the following speakers:
- Andre B. Argenton, chief sustainability officer and vice president of EH&S, Dow, Inc. (Midland, Mich.)
- Zhanna Golodryga, executive vice president, emerging energy and sustainability, Phillips 66, Inc. (Houston)
- Suresh Kotha, chief information officer, Sacramento Municipal Utility District (SMUD)
- Aqil Jamal, chief technologist, carbon management research division, Aramco (Riyadh, Saudi Arabia)
- Darryl Willis, corporate vice president, energy & resources industry, Microsoft (Redmond, Wash.)
- Mike Train, senior vice president and chief sustainability officer at Emerson (St. Louis, Mo.)
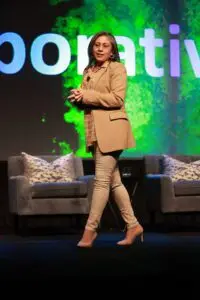
AspenTech’s Rasha Hasaneen led a panel of sustainability experts to discuss decarbonization trends and current priorities (Photo: AspenTech)
The panel opened with speakers highlighting some of the decarbonization and circularity initiatives that their organizations are prioritizing.
“What do we need to do to continue to decarbonize our industry? It’s a profound responsibility, and as as process engineers, we understand molecules better than anyone else. There are three main things to take advantage of: engineering expertise, physical assets and data technology,” stated Phillips 66’s Golodryga. As an example of her company’s sustainability progress, she highlighted Phillips 66’s work on the Rodeo Renewed Energy Complex near San Francisco, Calif., which is now processing only renewable feedstocks following a conversion from traditional fossil-fuels. “It’s operating at 30,000 barrels per day today of renewable diesel. By the end of the second quarter, we’ll bring it up to 50,000 barrels per day. And then at the end of this year, we’re going to be producing about 10,000 barrels per day of sustainable aviation fuel,” said Golodryga. “We’re committed to Scope one, two and three emission reductions. For Scope one and two, we want to be 30% reduction by 2030, and for Scope three 15%. We’ll continue to look at our assets to see how we can decarbonize them as much as possible bringing in renewable power where we can. For example, the Rodeo Refinery has a solar farm next to it.”
For SMUD, Kotha highlighted the group’s plans to decarbonize its five power plants. “We are focused on eliminating greenhouse-gas emissions from our generation portfolio by replacement, retooling or using clean, renewable fuels, like biomass or hydrogen. And another area is expanding our existing proven clean-energy technologies like solar, wind, hydro, biomass or geothermal energy storage. However, these clean-energy technologies wouldn’t be able to fully achieve zero carbon, but they will help us get there 90%.” To further progress, he emphasized SMUD’s work on piloting and scaling up emerging technology programs, such as long-duration battery storage, hydrogen and carbon capture and sequestration (CCS).
“We are laser focused on ensuring achieving that this zero-carbon plan comes at a reasonable cost that ensures it minimizes the rate increases to our customers. Our plan is to look for savings through operational excellence and pursuing grants at the federal and state level, as well as from partnerships,” he adds. SMUD has been awarded a $50-million grant from the Department of Energy’s Grid Resiliency and Innovation Program to support advanced grid technologies. “The last and most important area is maximizing the community benefits to improve the local air quality and the overall health of our regional community and, at the same time, creating cleantech jobs supporting disadvantaged communities.”
Argenton described Dow’s goals-oriented approach to decarbonization. “Let the engineers do what we do best. We create mathematical models that describe a process, and we use this model to look at fundamentals, and technical and economic feasibility. We’ve concluded that the biggest CO2-reduction return on investment comes for us in going after large projects. One example is our Alberta project, where we are building — a first in the chemical sector — world-scale net-zero-carbon-emissions cracker and ethylene derivatives plant. It’s new, it’s unique, and it’s approved by the Board,” said Argenton. Highlighting the benchmarks that make the Alberta project stand out, he mentions that the project employs a variety of clean and emerging technologies, including autothermal reforming, CCS and hydrogen.
He also noted that Dow has committed to a 2030 implementation of the first small modular nuclear reactor in a chemical plant. “The small modular nuclear reactors will bring an additional 400,000-ton reduction in CO2 emissions.”
When considering the sustainability challenges surrounding plastic waste and circularity of materials, Argenton says that the approach differs somewhat from typical decarbonization strategies. “When you are considering Scope 1 and 2 emissions for decarbonization, you can draw up the control volume of your plant, and then it’s a relatively simple model to determine where the supply and control volume starts. With materials, it involves consumer households, the sorting and cleaning of waste, as well as the eventual conversion of waste into new feedstock for the chemical sector.” In order to tackle these complexities, he emphasizes that cross-industry partnerships are key, highlighting Dow’s work with WM, which involves a nearly $1 billion investment by 2025 to significantly increase waste sorting and collection infrastructure, as well as Dow’s partnerships with Mura Technology to construct a large-scale advanced recycling plant in Germany and Procter and Gamble, which will involve the development of an all-new recycling technology.
Further underlining the essential role of cross-industry collaboration were several examples from Aramco. “The partnership and co-innovation approach is critical to bringing about decarbonization in the timeframe we’re talking about, and when considering all the different pathways to net zero,” said Jamal. He specifically mentioned joint work between Aramco, AspenTech and the Korea Advanced Institute of Technology to develop a software package focused on simulation and modeling of carbon-capture and utilization strategies. Jamal also discussed some of Aramco’s ongoing research in the field of carbon capture, which takes advantage of artificial intelligence (AI) and machine learning (ML). “We are already adopting AI and ML in materials discovery for direct-air capture of CO2. We have developed what may be the largest database ever for these different materials, and there is one hidden material somewhere that we will find, hopefully soon, through these AI/ML approaches. The material costs for direct-air capture is going to be key to viability, and if we can discover materials that can last longer and that have higher affinity for CO2 capture, then that will bring down costs significantly,” he explained. Aramco is partnering with Siemens Energy on a direct-air capture pilot plant to improve the practicality and reduce the costs associated with direct-air capture..
In another example of digital technology contributing to operational efficiency and sustainability, Jamal mentioned Aramco’s in-house predictive-modeling platform that considers weather and environmental events, such as dust storms and changing humidity levels, to help evaluate renewable-power yields and energy-storage needs. “We are investing in a lot of research in the area of energy storage. We’re working on flow-battery technologies, which we demonstrated recently in one of our facilities at a kilowatt scale. Now we are scaling up to megawatt-hour scales,” he added.
AI, and other digital technologies, including cloud platforms and advanced process models are clearly key pieces of the decarbonization puzzle. “I believe that AI will have a role in making sure everyone has a fair shot at clean, affordable, reliable electricity. We see AI as an accelerator to energy access. Ultimately, it’s contributing to the decarbonization of the system longer term. We also think that you cannot get there without the cloud,” said Darryl Willis of Microsoft. “There are all kinds of applications I see where we are in this we might apply digitalization to the energy sector, whether it’s around prescriptive maintenance, risk management, reservoir simulation or interpretation of geophysical bounds or other geological data, emissions management, cyber activity training, supply-chain optimization — these are all places where AI will totally transform what’s being done. We will totally reimagine the work that is getting done across the energy system. And I believe that it can’t help but accelerate the quality of the molecules and electrons that are being created,” he added.
Microsoft’s sustainability strategy includes plans to run all of its data centers and all of its operations on renewable power by 2025 and to be net zero by 2030. “The reality is that as big as Microsoft is — a $3-trillion company with 200,000 people around the world — we can’t do it by ourselves. You have to do it in coordination with partners. This is the accelerator that allows us to do everything we need to do,” noted Willis.
The panel ended with optimism for the future due to the technological resources — from AI to quantum computing — and co-innovation currently at play in the industry. “I think these next 10 years for automation are going to be amazing. We have to do it carefully. We have to do it safely. We have installed operations all over the world that we have to bring that with us, but at the same time, we can continue to push the envelope. I think a really exciting work that we see with customers is when they work on the roadmaps for very specific and innovative facilities, and when they start to implement those projects through the automation, we can really see the results,” said Mike Train of Emerson. ♦